The amendments to SOLAS II-1/3-8 introduce new requirements and guidelines for the strength, arrangement, and maintenance of towing and mooring equipment. These are detailed in the following paragraphs:
Many vessels now are required to have their existing mooring and towing equipment undergo annual thorough examinations. In the same way all lifting accessories have these inspections and certification to ensure their suitability, reduce the likelihood of failure and increase the life span of the equipment onboard.
Yachts have vastly different itineraries so the equipment will experience varied amounts of stress and load cycling. A “high use” world cruising charter vessel will see completely different wear and tear on their mooring lines when compared to a single season boat that spends most of its life docked in nice marinas. Condition based analysis should be performed to make sure that healthy rope is not wasted but tired rope is decommissioned before the event of a failure.
Examinations can be performed onboard or at one of our facilities where our rigging and load testing surveyors can advise on the best action. This is commonly tied in with yachts annual lifting equipment survey and load testing. Along with thorough examinations, RSB offers vessel branded durable soft labels and/or NFC tags, colour coding, digital or physical certification and defect reports along with cover repairs or additional chafe protection where the wear is only superficial.
New mooring lines and towing systems should have manufacturer traceability along with verified break loads. Each individual line should be labelled with the length, date of manufacture, break load / WLL and a reference code that corresponds to the mooring plan.
Areas where chafe and major deflection are present should be reinforced with additional hard-wearing materials such as Dyeema, leather or similar products. Short sacrificial loops that can be replaced on a regular basis can be integrated to protect the expensive mooring line from unnecessary wear caused by rough marina bollards.
Dyneema mooring lines are ever more common onboard larger yachts as their strength to weight (and size) ratio is unrivalled and reduces the amount of effort needed to rig up. These ropes are static and have very little elastic properties, so it is essential to use a dynamic stretcher tail around the dockside bollard. This will minimise wear on the main mooring rope but also reduce snatching and stress on the vessels structure.
If you need durable floating line with rugged loops to moor stern to the rocks in Croatia, budget friendly options for low season or luxury aesthetic lines that look like masterpieces we offer the highest quality SOLAS approved mooring solutions, a variety of materials and colours, hand crafted and tailored to the vessels needs.
Key definitions
To better understand these regulations, some key definitions are explained:
- Safe Working Load (SWL) means the safe load limit of shipboard fittings used for mooring operations in harbours or similar sheltered waters.
- Safe Towing Load (TOW) means the safe load limit of shipboard fittings used for normal and other towing.
- Ship Design Minimum Breaking Load (MBLSD) means the minimum breaking load of new, dry mooring lines for which shipboard fittings and supporting hull structures are designed to meet mooring restraint requirements.
- Line Design Break Force (LDBF) is the minimum force at which a new, dry, spliced mooring line will break. It is for all synthetic cordage materials
Practical impact for existing ships
Ship operators will need to review their existing safety management systems related to mooring lines and mooring equipment onboard and check compliance with MSC.1/Circ.1620. Due to the required documentation, MBLSD should be established as the replacement lines should have a LDBF 100-105% of MBLSD. MBLSD might be determined based on mooring arrangement plans. Also, the number of mooring lines onboard should match the original concept.
For ships with the keels laid before 1 January 2007 and without appropriate documentation, owners may establish the MBLSD for mooring based on the safe working load of mooring equipment provided on board. If no safe working load is specified, owners are advised to check the strength of mooring equipment and their supporting hull structure based on MSC.1/Circ.1175/Rev.1 and determine MBLSD based on the actual capacity of mooring equipment and the supporting hull structure.
The records of inspection and maintenance of mooring equipment
The records of inspection and maintenance of mooring equipment, inspection and replacement of mooring lines, since the last periodical survey, should be kept updated and available on board and will be subject for periodical survey.
Management plans for inspection and maintenance of mooring equipment:
- Procedures for mooring operations, inspection, and maintenance of mooring equipment, including mooring lines.
- Procedures to allow the identification and control of mooring lines, tails and associated attachments.
- Periodic inspection of mooring lines, mooring line tails and associated attachments as part of the onboard maintenance plan or equivalent maintenance management system.
- Manufacturersʹ criteria for replacement of mooring lines should be available.
- Records of the original design concept, equipment, arrangements, and specifications should be available on board.
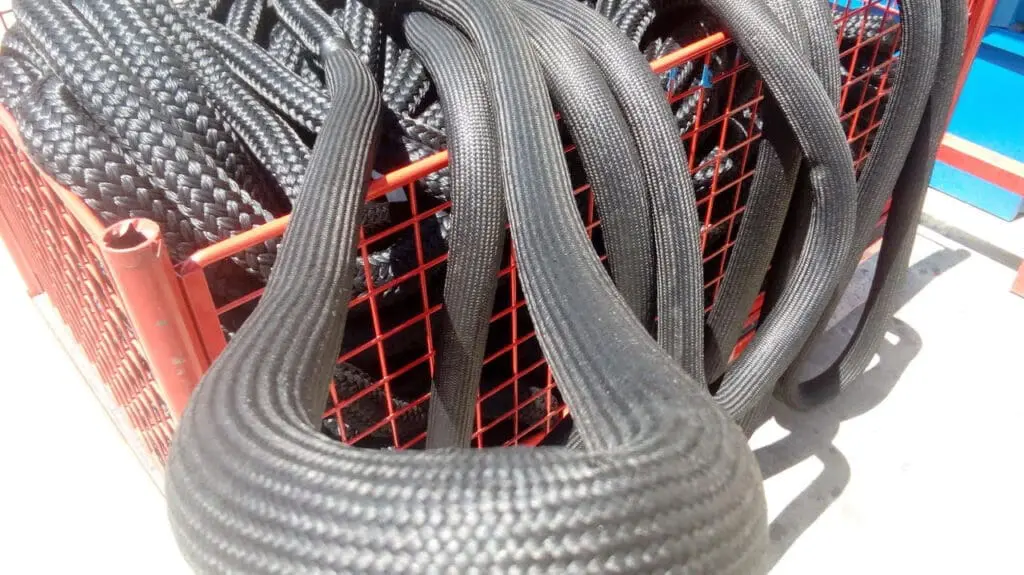
Mooring lines and fittings:
Technical specification documents of the mooring lines provided onboard must include information such as the number of mooring lines, recommended minimum diameters (D) for fittings in contact with mooring lines, Line Design Break Forces (LDBF) for mooring lines, and properties related to the bend radius (D/d ratio) of mooring lines. LDBF should fall within the range of 100-105% of MBLSD , or 105% of SWL if higher, when selecting mooring lines. The selection of mooring lines and fittings should consider the diameter (D) of surfaces of mooring fittings in relation to the mooring line diameter (d) (i.e., the D/d ratio) to minimize potential strength loss caused by the mooring line bending.
Markings on mooring fittings:
Ships with the keels laid on or after 1 January 2007 must clearly mark each fitting or item of equipment, including bollards, fairleads, rollers, and mooring winches, with any limitations associated with its safe operation.
The records of inspection and maintenance of mooring equipment
The records of inspection and maintenance of mooring equipment, inspection and replacement of mooring lines, since the last periodical survey, should be kept updated and available on board and will be subject for periodical survey.
Mooring winches:
The holding capacity of winch brakes should not exceed 100% of MBLSD. Mooring winch brakes should enable the reliable setting of the operational brake rendering load.